從設計到生產 確保產品可製造性的全方位指南
您是否曾因為產品設計與生產之間的落差而感到困擾?產品設計再精美,若無法順利量產,一切努力都將付諸流水。這篇文章將帶您深入了解如何從設計之初就考慮可製造性,有效降低生產成本,提升產品品質,並縮短產品上市時間。讀完本文,您將能:
- 掌握設計階段考量可製造性的關鍵技巧
- 了解不同生產流程對產品設計的影響
- 學習如何有效與製造團隊溝通協作,確保生產順利進行
讓我們一起探索確保產品可製造性的全方位策略!
設計階段的可製造性分析 (DFMA)
產品可製造性的關鍵在於設計階段。DFMA (Design for Manufacturing and Assembly) 是一種系統化的流程,旨在在設計階段就評估產品的可製造性和組裝性。有效的 DFMA 能夠在產品進入生產階段前,即發現並解決潛在的製造問題,避免後續的成本增加和時間延誤。DFMA 的核心步驟包括:
- 材料選擇:選擇易於加工、成本效益高且符合產品性能要求的材料。考慮材料的加工特性、供應鏈穩定性以及環保因素。
- 零件設計:簡化零件設計,減少零件數量,並選擇標準化零件。避免使用複雜的幾何形狀和難以加工的結構。設計時應考慮零件的加工精度、公差範圍和表面處理要求。
- 組裝設計:簡化組裝流程,減少組裝步驟,並設計易於組裝的結構。使用模組化設計,將產品分解成易於管理和組裝的模組。考慮組裝工具和設備的選擇。
- 製造流程分析:評估不同的製造流程,選擇最經濟高效的方案。考慮不同流程的成本、生產效率、品質控制以及環境影響。
與製造團隊的溝通協作
設計團隊與製造團隊之間的有效溝通協作是確保產品可製造性的關鍵。設計團隊需要及時向製造團隊提供設計圖紙、規格說明和相關文件。製造團隊則需要提供設計可行性分析和製造建議。雙方需要定期溝通,及時解決設計和生產中出現的問題。
生產階段的品質控制
生產階段的品質控制對於確保產品可製造性至關重要。有效的品質控制系統能及時發現並解決生產過程中出現的問題,確保產品符合設計要求和品質標準。品質控制的措施包括:
- 進料檢驗:對生產過程中使用的原材料進行檢驗,確保其符合品質要求。
- 過程控制:對生產過程中的各個環節進行監控,確保生產過程符合標準。
- 成品檢驗:對生產完成的產品進行檢驗,確保其符合設計要求和品質標準。
常見問題與解決方案
在產品生產過程中,常常會遇到一些常見的問題,例如:零件加工精度不足、組裝困難、產品性能不穩定等等。針對這些問題,我們需要採取有效的解決方案,例如:優化設計、調整製造流程、改進品質控制等等。
案例分析:一個成功的產品可製造性案例
一家電子產品公司在開發新產品時,充分考慮了產品的可製造性。他們在設計階段就進行了詳細的 DFMA 分析,選擇了易於加工的材料,簡化了零件設計和組裝流程。在生產階段,他們建立了嚴格的品質控制系統,及時發現並解決了生產中出現的問題。結果,該產品的生產效率得到了提高,產品品質得到了保證,產品上市時間也得到了縮短。這個案例說明,有效的產品可製造性管理能為企業帶來巨大的效益。
持續改進與創新
確保產品可製造性是一個持續改進的過程。隨著技術的進步和市場需求的變化,我們需要不斷改進產品設計和製造流程,以提高產品的可製造性。
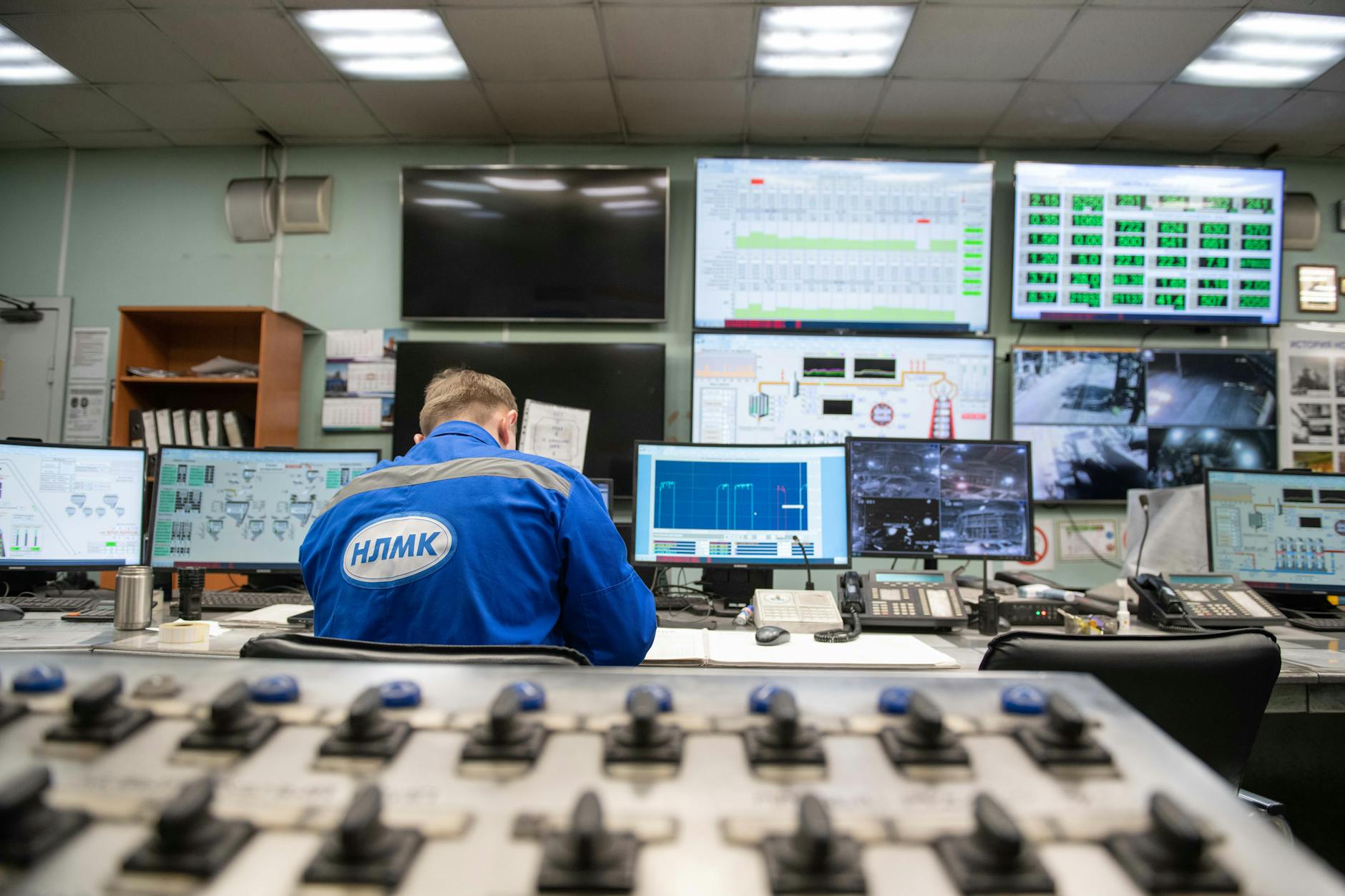
總結
確保產品可製造性是一個系統工程,需要設計團隊、製造團隊和品質控制團隊的共同努力。通過有效的 DFMA 分析、良好的溝通協作和嚴格的品質控制,我們可以有效地提高產品良率,降低生產成本,縮短產品上市時間,並提升產品競爭力。
步驟 | 說明 | 注意事項 |
---|---|---|
設計階段 | 進行DFMA分析,選擇合適材料,簡化設計 | 避免複雜結構,使用標準化零件 |
生產階段 | 建立嚴格品質控制系統 | 及時發現並解決問題 |
溝通協作 | 設計團隊和製造團隊保持良好溝通 | 及時反饋,共同解決問題 |
常見問題 (FAQ)
什麼是DFMA?
DFMA (Design for Manufacturing and Assembly) 是設計製造與組裝的縮寫,是一種系統化的流程,旨在在設計階段就評估產品的可製造性和組裝性,以降低生產成本和時間。
如何選擇合適的材料?
選擇材料時需要考慮材料的加工特性、成本、供應鏈穩定性、產品性能要求以及環保因素。
如何提高產品的組裝性?
提高產品組裝性需要簡化組裝流程,減少組裝步驟,並設計易於組裝的結構,例如使用模組化設計。
如何進行有效的品質控制?
有效的品質控制需要在進料、過程和成品三個階段進行檢驗,並建立完善的品質管理體系。
如何與製造團隊有效溝通?
設計團隊和製造團隊需要定期溝通,及時反饋設計和生產中的問題,並共同尋找解決方案。