您是否正在為產品設計與生產的可製造性問題而苦惱?讀完本文,您將能:
- 了解確保產品可製造性的五大關鍵考量
- 掌握提升產品生產效率和降低成本的方法
- 學習如何從設計階段就開始考慮可製造性
讓我們深入探討!
產品可製造性定義與重要性
產品可製造性 (Design for Manufacturing, DFM) 指的是在產品設計階段就考慮到生產過程中的各種因素,以確保產品能夠以高效、低成本、高品質的方式生產。一個具有良好可製造性的產品,通常具有以下特點:生產流程簡單、生產週期短、生產成本低、產品品質穩定、良率高。忽略產品可製造性,可能導致生產成本過高、生產效率低下、產品品質不穩定,甚至產品無法生產。
五大關鍵考量 確保產品可製造性
從設計到生產,確保產品可製造性需要考慮多個方面。以下列出五大關鍵考量,並深入探討:
1. 材料選擇
材料選擇是影響產品可製造性的首要因素。需要考慮材料的成本、性能、可加工性、供應穩定性等因素。選擇易於加工、成本低廉、性能滿足需求的材料,可以有效降低生產成本和提升生產效率。例如,選擇容易塑膠射出成型的材料,可以有效縮短生產週期。
2. 製程設計
製程設計指的是產品的生產流程設計。一個良好的製程設計,應該簡單、高效、可靠。需要考慮生產設備的可用性、生產人員的技能水平、生產環境等因素。例如,可以採用模組化設計,將產品分解成多個模組,以便於生產和組裝。此外,需要考慮製程的自動化程度,以提高生產效率和降低生產成本。一個設計良好的製程,可以有效減少生產錯誤,提升產品良率。
3. 公差控制
公差控制指的是對產品尺寸、形狀、位置等方面的精度控制。公差過小,會增加生產難度和成本,甚至導致產品無法生產;公差過大,則會影響產品的性能和品質。因此,需要根據產品的功能要求和生產能力,合理設定公差,並制定有效的公差控制措施。例如,可以採用精密的數位控制加工設備,以確保產品的精度。
4. 組裝流程
組裝流程是指產品各個零件的組裝過程。一個良好的組裝流程,應該簡單、高效、可靠。需要考慮零件的尺寸、形狀、重量、材質等因素,以及組裝設備的可用性、組裝人員的技能水平等因素。例如,可以採用自動化組裝設備,以提高組裝效率和降低組裝成本。此外,需要設計簡潔的組裝流程,減少組裝步驟,並避免使用過多的螺絲或其他緊固件。
5. 測試驗證
測試驗證指的是對產品進行測試,以驗證產品是否符合設計要求和性能指標。測試驗證應該在產品生產的不同階段進行,包括設計驗證、工藝驗證和產品驗證。需要制定有效的測試方案,並使用精密的測試設備,以確保測試結果的準確性和可靠性。測試驗證可以有效發現產品設計和生產過程中的缺陷,並及時糾正,以提升產品品質和降低生產成本。
案例分享:提升產品可製造性的實務經驗
我們曾協助一家電子產品公司提升其產品的可製造性。通過優化材料選擇、簡化製程設計、精確公差控制、改進組裝流程和完善測試驗證流程,該公司成功將產品生產效率提升了 30%,並降低了 15% 的生產成本。
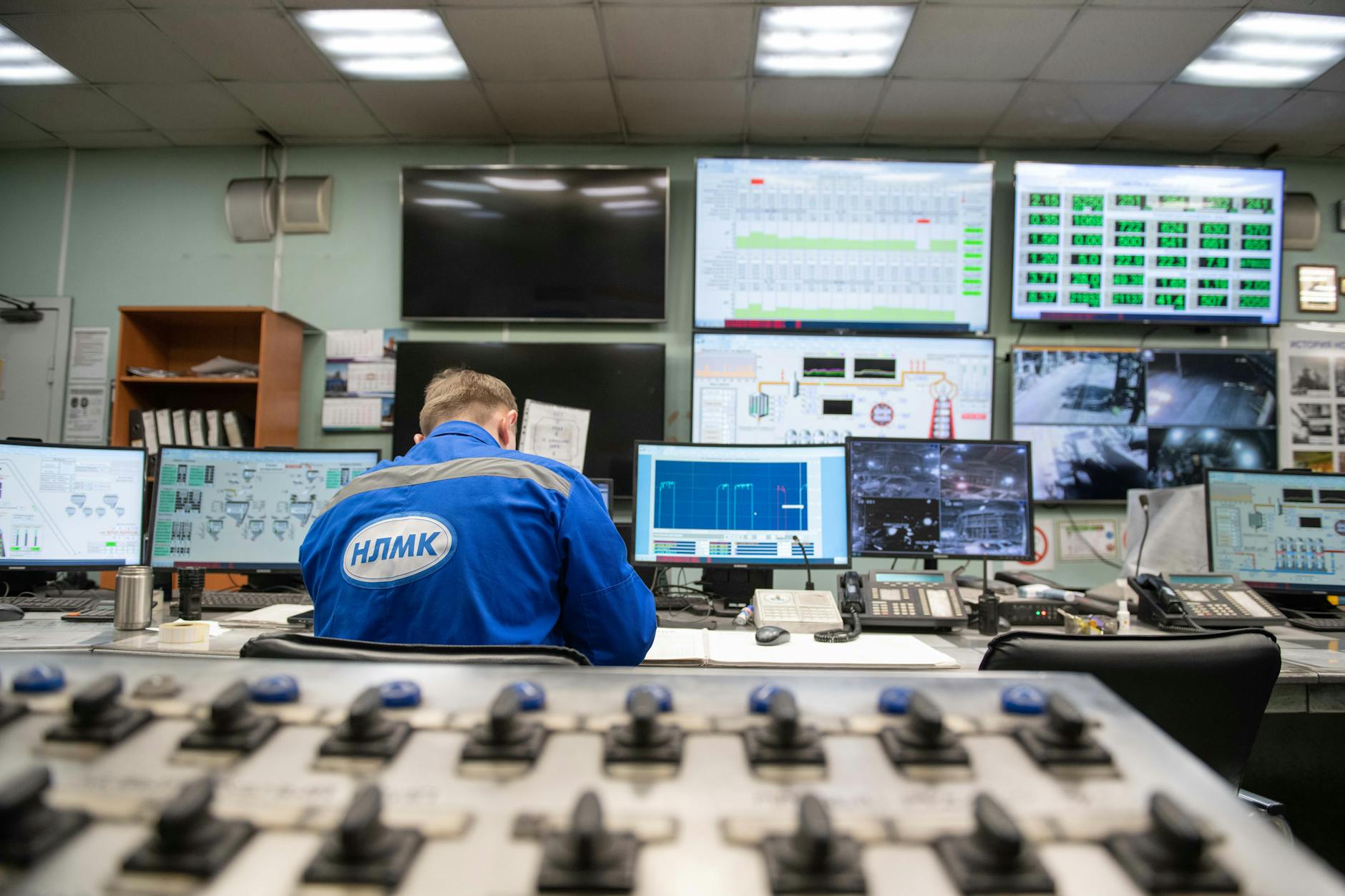
結論
確保產品的可製造性,需要從設計階段就開始考慮,並在生產過程中進行嚴格的控制。通過合理的材料選擇、製程設計、公差控制、組裝流程和測試驗證,可以有效提升產品生產效率、降低生產成本、提升產品品質。希望本文能幫助您更好地了解產品可製造性,並在產品設計與生產過程中有所應用。
常見問題 (FAQ)
如何評估產品的可製造性?
可以通過DFM分析,評估產品設計的可製造性,例如使用DFMA(Design for Manufacturing and Assembly)軟體工具,評估零件數量、組裝複雜度、材料成本等因素。
DFM分析的工具有哪些?
市面上有很多DFM分析工具,例如CAD軟體內建的DFM模組,或獨立的DFM軟體,例如SolidWorks、Autodesk Inventor等。
如何提升產品的組裝效率?
可以通過模組化設計、簡化組裝步驟、使用自動化組裝設備等方法來提升產品的組裝效率。
如何控制產品的公差?
需要根據產品的功能要求和生產能力,合理設定公差,並制定有效的公差控制措施,例如使用精密的數位控制加工設備,並進行嚴格的檢驗。
測試驗證的重要性是什麼?
測試驗證可以有效發現產品設計和生產過程中的缺陷,並及時糾正,以提升產品品質和降低生產成本,確保產品符合設計要求和性能指標。