精實生產線 減少浪費 從根本檢討
您是否正為生產線上的浪費問題感到困擾?生產成本居高不下?產品交期一再延誤?讀完本文,您將能:
- 了解精實生產的七大浪費及其影響
- 掌握從生產線檢討精實原則的實務方法
- 學習如何導入精實生產並持續改善
- 獲得提升生產效率和降低成本的實務策略
讓我們深入探討如何透過檢討精實生產線原則,有效減少浪費,建立高效益的生產系統。
精實生產與浪費的關係
精實生產 (Lean Manufacturing) 的核心概念是最大限度地減少浪費,以提高效率和生產力。在精實生產系統中,任何不能為客戶創造價值的活動都被視為浪費。這些浪費不僅會增加成本,還會降低產品品質和客戶滿意度。常見的七大浪費包括:
- 過度生產 (Overproduction): 生產過多的產品,導致庫存積壓。
- 等待 (Waiting): 材料、設備或人員等待,造成時間和資源的浪費。
- 搬運 (Transportation): 材料和產品的非必要搬運,增加成本和時間。
- 加工過度 (Over-processing): 使用過多的加工步驟,增加成本和時間。
- 庫存 (Inventory): 過多的庫存,佔用空間和資金。
- 動作 (Motion): 人員的非必要動作,降低效率。
- 瑕疵 (Defect): 產品瑕疵,導致返工、報廢和客戶抱怨。
減少浪費不只是降低成本,更能提升生產流程的效率,讓企業更具競爭力。
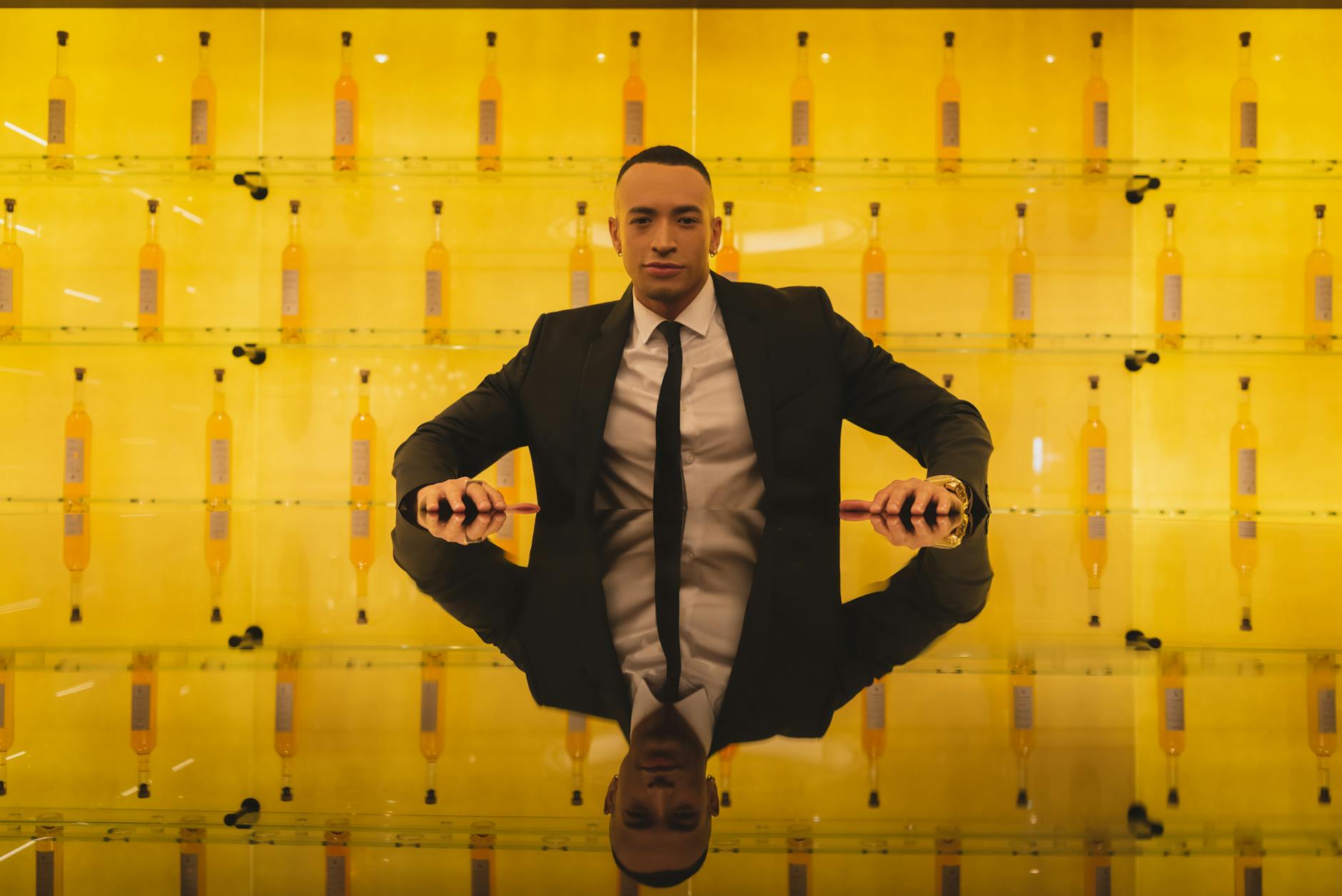
從生產線檢討精實原則的步驟
要有效減少生產線上的浪費,需要系統性的檢討和改善。以下步驟可以作為參考:
- 識別浪費: 首先,需要對生產線進行全面的評估,識別出所有形式的浪費。可以使用價值流程圖 (Value Stream Mapping) 等工具來協助識別浪費。
- 量化浪費: 確定每種浪費的數量和成本,以便評估其對生產效率的影響。
- 分析根本原因: 深入分析浪費的根本原因,找出問題的根源,而不是只處理表面現象。
- 制定解決方案: 根據分析結果,制定有效的解決方案,例如改善流程、導入新技術或培訓員工。
- 實施和監控: 實施解決方案,並持續監控其效果,確保其能有效減少浪費。
- 持續改善: 精實生產是一個持續改善的過程,需要不斷地檢討和改進生產流程,以達到更高的效率和生產力。
精實生產實務案例分析
以下是一些企業成功導入精實生產,減少浪費的案例:豐田生產系統 (TPS) 是精實生產的典範,透過看板系統、準時化生產等方法,有效減少庫存和等待時間。
許多製造業企業透過導入精實生產,成功降低成本、提升品質和生產效率。例如,某家電子製造商透過精實生產的改善,將生產週期縮短了30%,同時降低了15%的生產成本。
導入精實生產的挑戰與解決方案
導入精實生產的過程中,可能會遇到一些挑戰,例如員工的抗拒、缺乏管理支持和缺乏適當的工具和技術。為了克服這些挑戰,企業需要:
- 獲得管理層的支持: 管理層的支持對於成功導入精實生產至關重要。
- 員工培訓: 員工需要接受適當的培訓,以了解精實生產的原則和方法。
- 導入適當的工具和技術: 使用價值流程圖、看板系統等工具,可以有效地識別和減少浪費。
- 持續改善: 精實生產是一個持續改善的過程,需要不斷地檢討和改進生產流程。
精實生產與其他管理方法的比較
方法 | 重點 | 優點 | 缺點 |
---|---|---|---|
精實生產 | 減少浪費,提高效率 | 降低成本,提高品質,縮短交期 | 需要持續的改善,員工需要接受培訓 |
六標準差 | 減少變異,提高品質 | 提高產品品質,降低缺陷率 | 需要大量數據分析,耗時費力 |
全面品質管理 | 持續改進,顧客滿意 | 提高顧客滿意度,提升企業形象 | 需要全體員工參與,需要長期投入 |
結論
減少生產線上的浪費,是提升企業競爭力的關鍵。透過檢討精實生產原則,並採取系統性的改善措施,企業可以有效降低成本,提高效率和品質。持續改善是精實生產的核心精神,企業需要不斷地檢討和改進生產流程,以達到更高的效率和生產力。希望本文能幫助您在生產線上有效減少浪費,建立一個高效益的精實生產系統。
常見問題 (FAQ)
什麼是精實生產的七大浪費?
精實生產的七大浪費包括:過度生產、等待、搬運、加工過度、庫存、動作、瑕疵。
如何識別生產線上的浪費?
可以使用價值流程圖 (Value Stream Mapping) 等工具來協助識別浪費,並透過觀察和數據分析找出浪費的來源。
導入精實生產需要哪些步驟?
導入精實生產需要識別浪費、量化浪費、分析根本原因、制定解決方案、實施和監控,以及持續改善等步驟。
精實生產與其他管理方法有什麼不同?
精實生產與六標準差、全面品質管理等方法都有所不同,精實生產更著重於減少浪費,提高效率;六標準差則注重減少變異,提高品質;全面品質管理則強調持續改進,顧客滿意。
導入精實生產會遇到哪些挑戰?
導入精實生產可能會遇到員工抗拒、缺乏管理支持、缺乏適當工具和技術等挑戰。